ADVANCED CNC/PLASMA CUTTING SYSTEMS
A Cut Above the Rest
Let Us Help You Take Your Industrial Cutting to the Next Level
Plasma is a a very safe, efficient, and clean way to cut metal. It's key to have the right machine for the job, and know how to use it properly.
Plasma cutters use a beam of ionized gas or plasma to heat metal beyond its melting point and then blows away the melted material to reveal a hole or cut. The torch moves across the metal much like that of a saw blade. It can be done using a hand torch, however table-mounted systems equipped with a computer-controlled gantry offer several advantages including:
- rapid, repetitive cutting with a high degree of accuracy
- ability to replace tedious, multi-step cutting and drilling processes
- improved efficiency and fewer hours of layout work.
Some key facts about these systems:
- Arc can reach temperatures of 45,000 degrees F
- Have on/off switches and an amperage settings that determines how much power to use for cutting
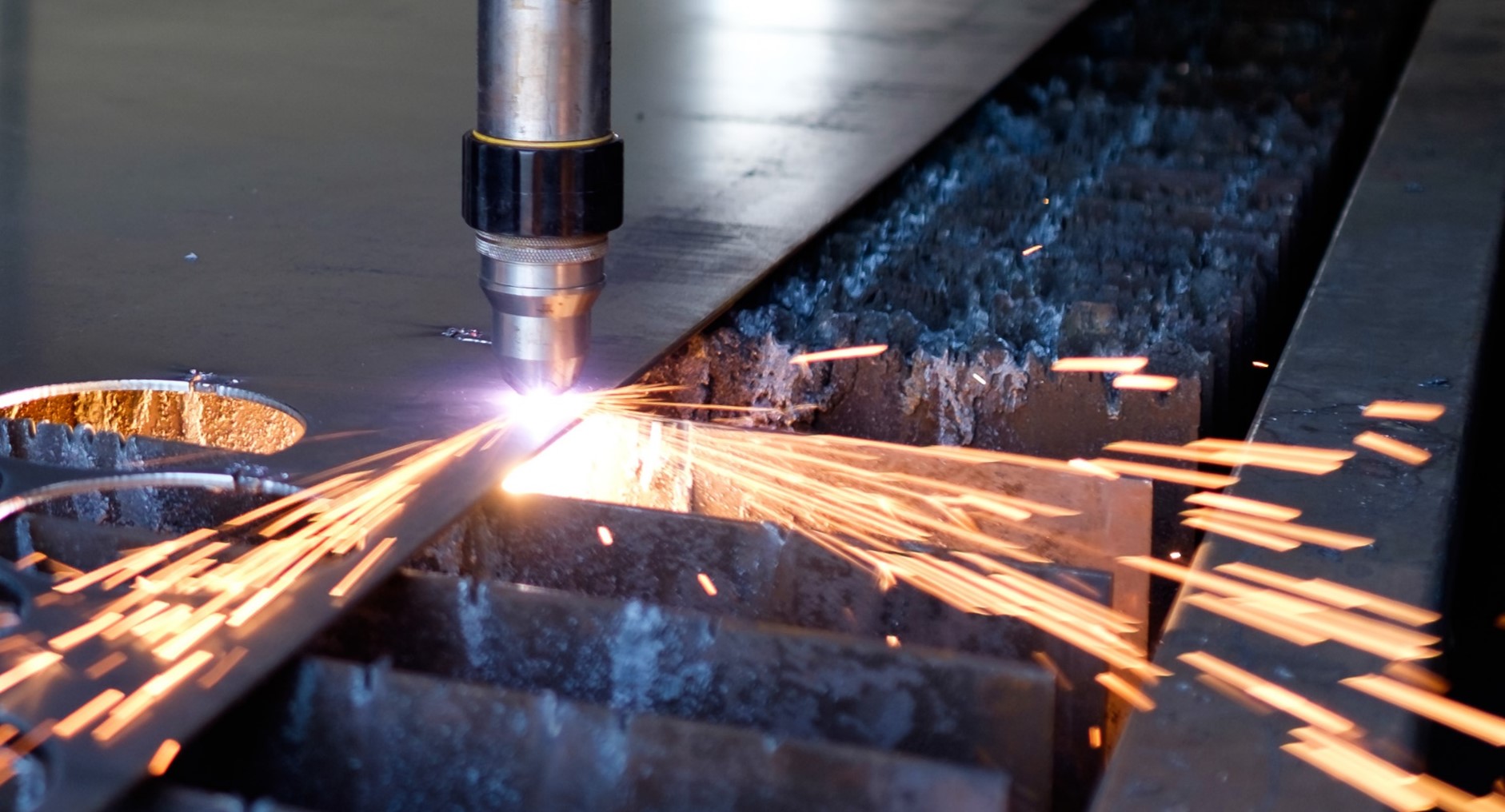
TYPES OF SYSTEMS
There are two main types of plasma cutting: standard and high definition (SD & HD, respectively). HD plasma cutters feature a different torch design and gas feed, give 1-3 degrees of cut bevel, virtually no dross, and make oxide-free cuts on mild steel. SD plasma gives 3-5 degrees of cut bevel, dross that needs cleaning prior to welding, and makes oxide-free cuts on stainless and aluminum.
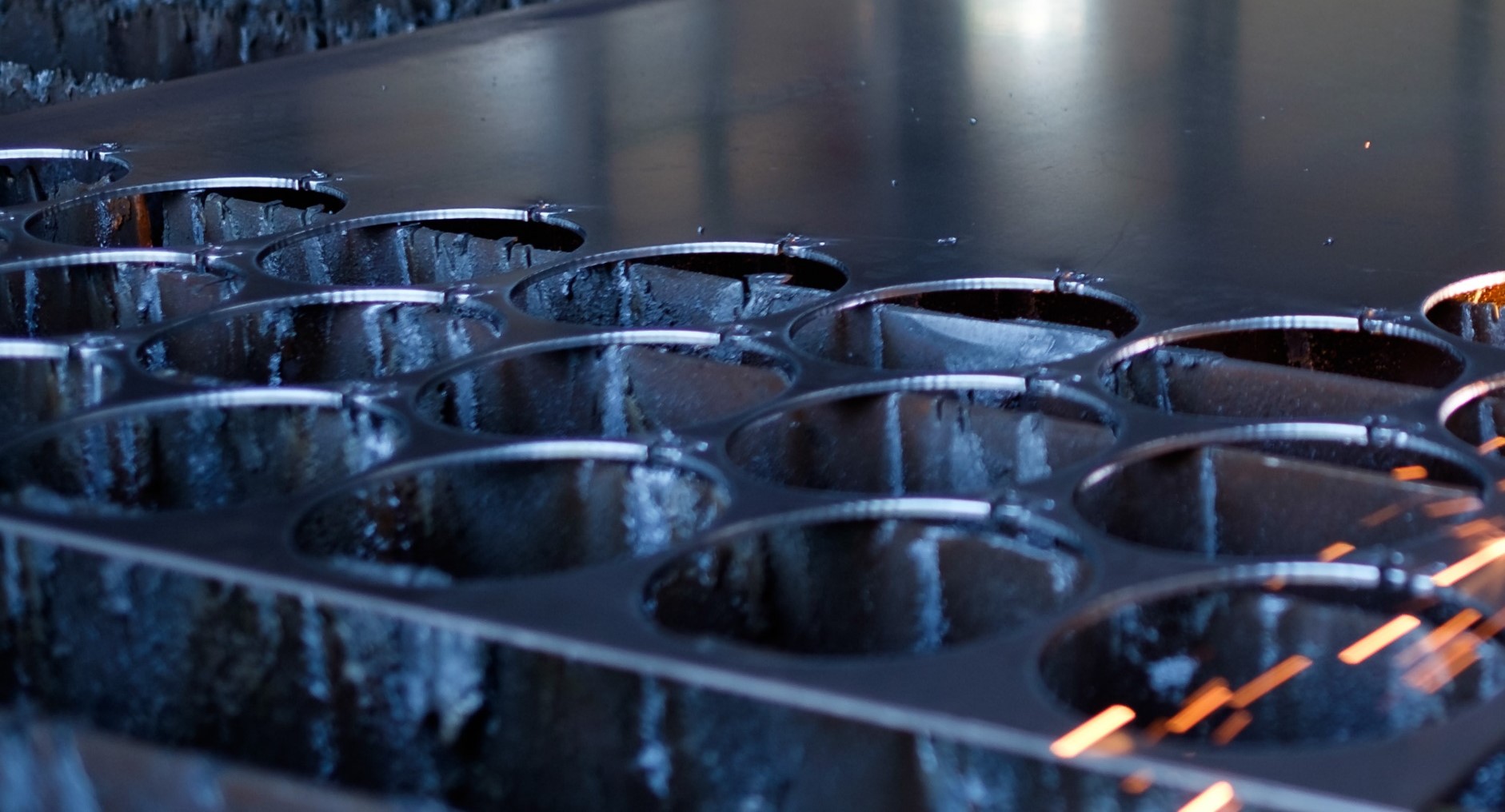
SYSTEM APPLICATIONS
Systems can cut simple or complex shapes into materials like common steels and aluminum, and virtually any material that conducts electricity. Some materials, such as those that create toxic fumes, can be cut with plasma cutting systems that incorporate venting, gas selection, and other special features.
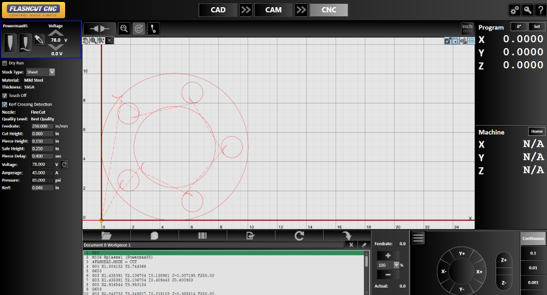
CUTTING SOFTWARE
CNC plasma cutting systems work in concert with software packages such as AutoCAD and Turbo CAD, using a universal export (interchange) format called DXF. Drawings created in a DXF format can be easily imported into most plasma cutting systems.

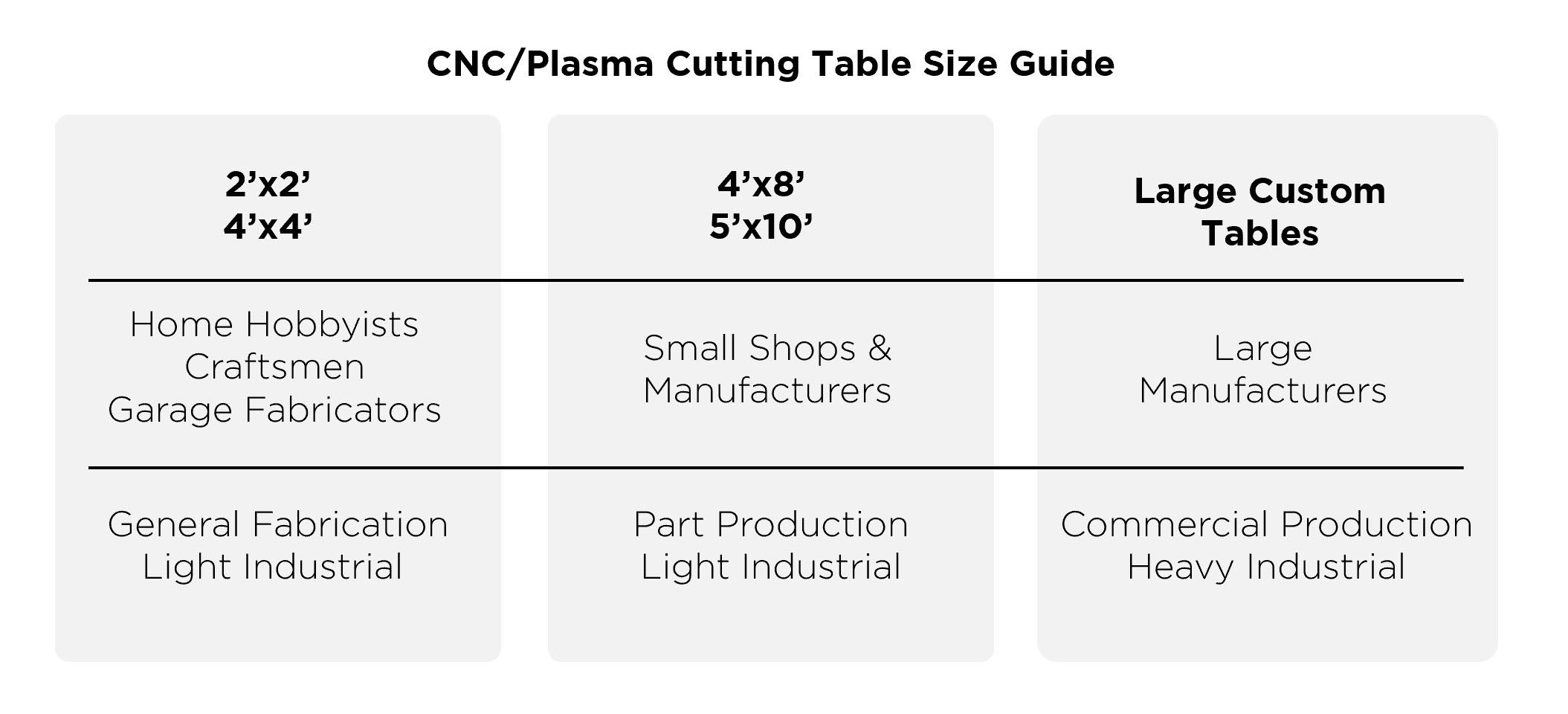